Automotive Transportation
Provide complete measurement and control equipment and integrated automation production line solutions focused on the electrification and intelligence of new energy vehicles
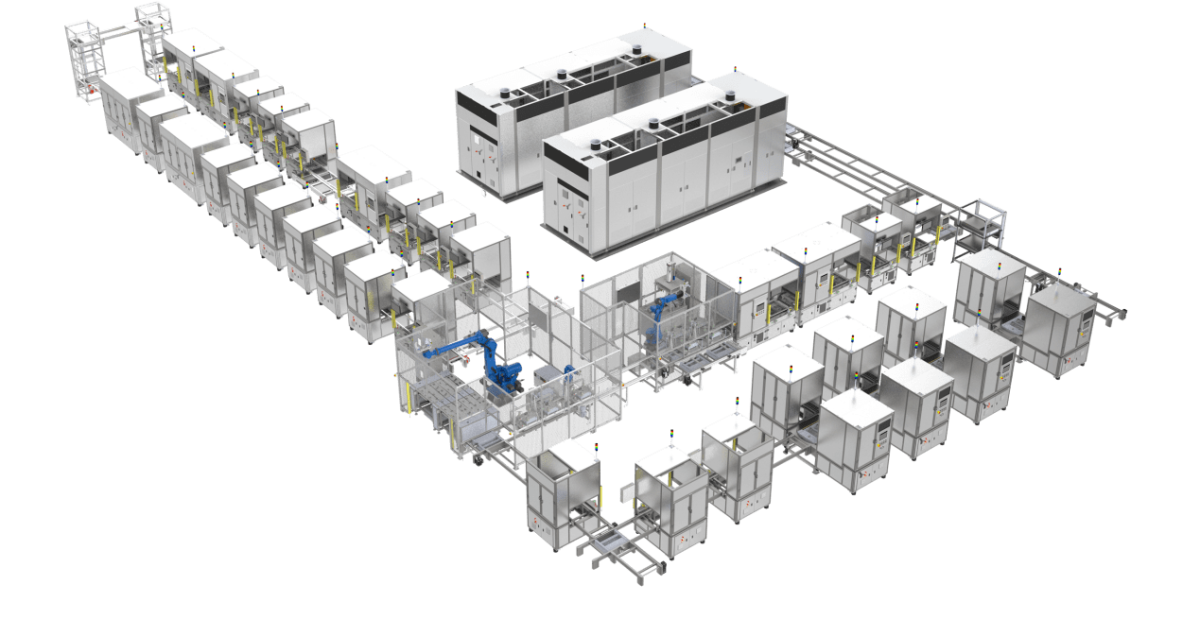
Electronic Control / Inverter Brick Assembly / Test Line
The assembly and test line for electronic control/inverter bricks of new energy vehicles realizes fully automated and flexible production, integrating processes such as loading and unloading, assembling, dispensing, potting, curing, testing, and aging. The whole line adopts a visual production kanban system to monitor the process in real time and record data throughout the process to ensure traceability. The flexible and quick-change design supports rapid adjustment to meet the efficient production needs of different products
Core Station Composition
Tightening, dispensing, curing, wave soldering, AOI (Automated Optical Inspection), airtightness testing, aging testing, safety regulation testing, EOL testing
Technical Highlights
Modular and flexible design, visualization, automatic screening of OK and NG products, and traceability of the source of defects
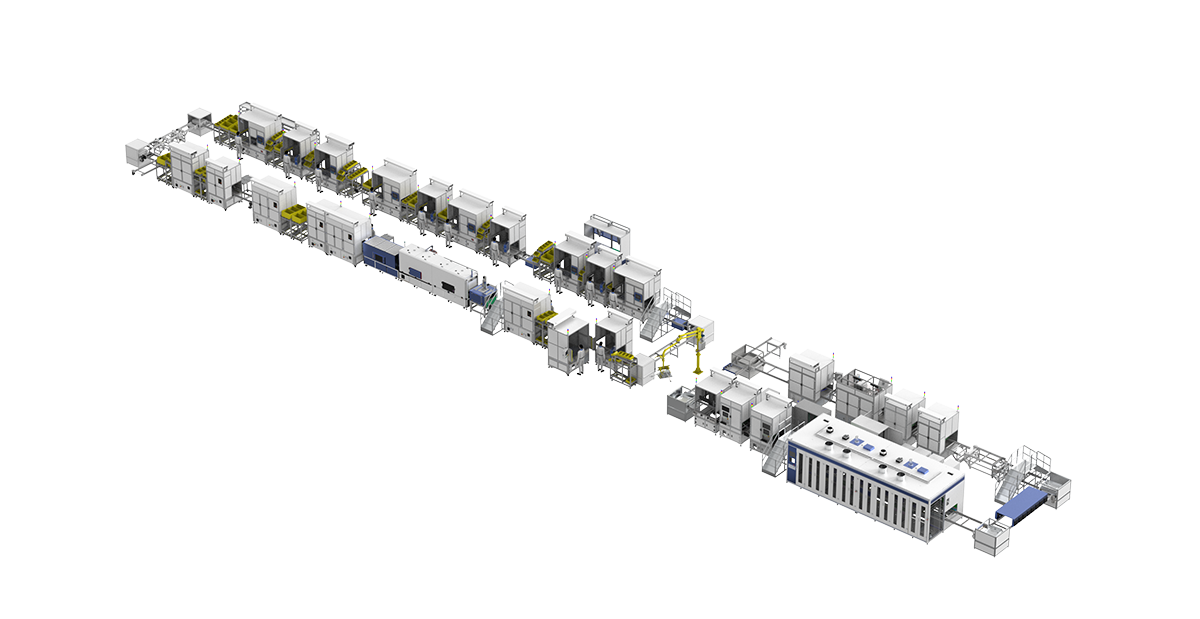
OBC DCDC Assembly / Test Line
The assembly and test line for new energy vehicle OBC/DCDC integrates mechanical, electrical and control technologies to realize the automatic transportation, assembly and detection of electronic control components. Through advanced equipment and strict testing, the product performance is comprehensively evaluated, such as data processing, power consumption, stability and reliability. The intelligent control system monitors and adjusts production parameters in real time to ensure that each product is assembled and tested under the best conditions, providing efficient guarantee for the production of new energy vehicles
Core Station Composition
Selective soldering, tightening, dispensing, curing, AOI (Automated Optical Inspection), three-proof coating, abnormal sound testing, safety regulation testing, calibration testing
Technical highlights
High-precision assembly, highly efficient automated production, flexible and customizable, intelligent management
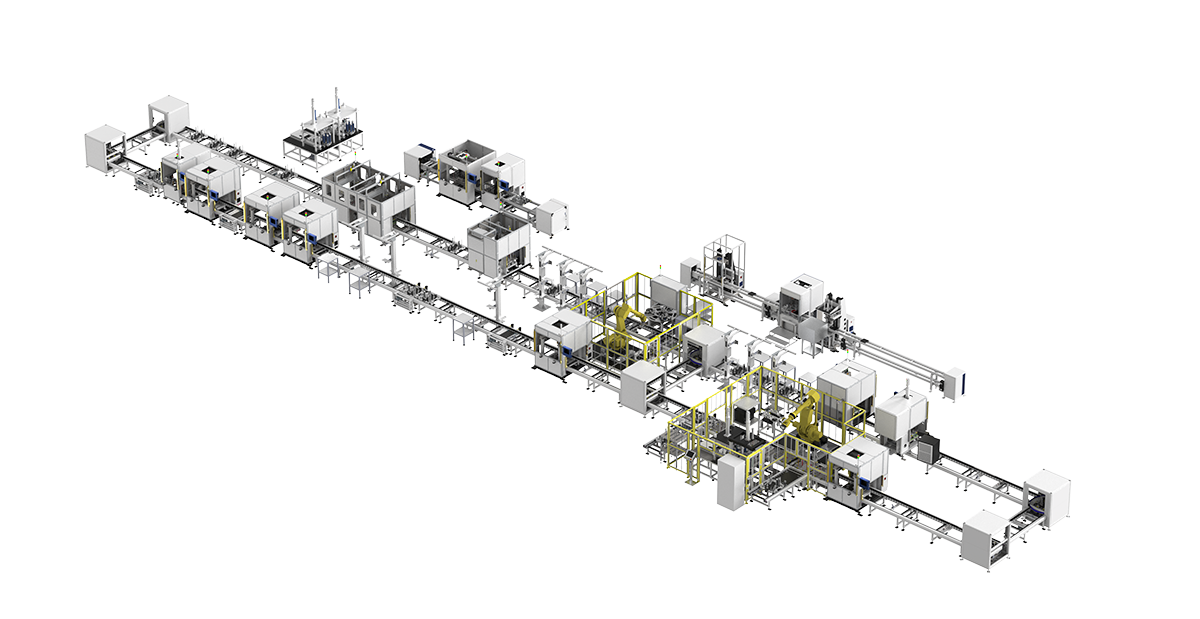
Electric Drive Assembly / Test Line
The electric drive assembly and test line for new energy vehicles integrates advanced automated assembly and detection technologies, covering processes such as assembly, press-fitting, tightening, oil injection, electrical performance detection, and EOL testing. Through a highly automated and flexible design, the whole line ensures efficient production and precise quality control. The intelligent production management system can monitor the production status in real time and dynamically adjust process parameters to ensure the assembly accuracy and reliability of products, providing a stable technical guarantee for the electric drive system of new energy vehicles
Core Station Composition
Starting resistance torque test, automatic press-fitting of elastic pins, heating equipment for driven gears, tightening of differential bolts, press-fitting of inner rings of differential bearings, differential, press-fitting of outer rings of secondary shafts, measurement and selection of shims, assembly of shaft systems into boxes, tightening of hydraulic modules, tightening of box bolts, oil injection and extraction and weighing, electrical performance testing, EOL testing
Technical Highlights
The assembly process is mainly automatic, and the automation rate of the production line is 80%. Two products can be switched for production
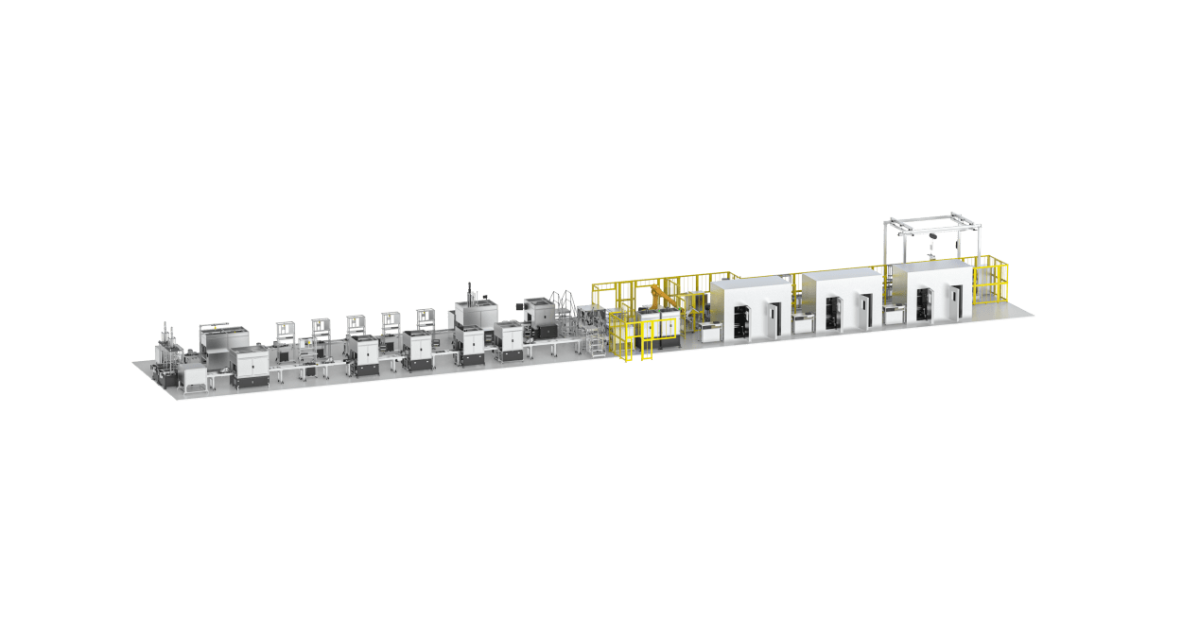
Electric Motor Assembly / Test Line
The electric motor assembly and test line for new energy vehicles has an annual production capacity of 150,000 flat wire motors. It adopts a modular and lightweight design and supports multi-linear production and rapid model change. The whole line integrates advanced automated technologies to ensure the accuracy and consistency of assembly and flexibly respond to different product requirements, improving production efficiency. It provides an efficient and reliable production solution for the power system of new energy vehicles
Core Station Composition
Riveting/pressing/dispensing of iron cores, stacking into shafts, dynamic balance testing, rotor into end cap, whole machine assembly, dispensing on housing, tightening of screws for assembly, dispensing on small end cap surface, heat shrinking stator, comprehensive testing, airtightness testing, no-load testing in a silent room
Technical Highlights
The assembly process is mainly automatic, and the automation rate of the production line is 85%. Three products can be switched for production
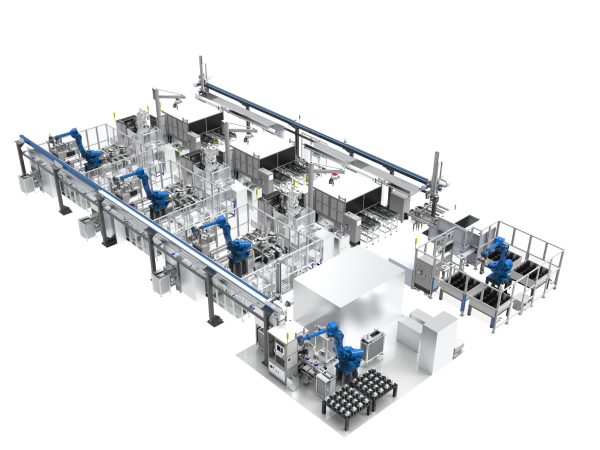
Rotor Assembly / Test Line
The rotor assembly and test line for new energy vehicles adopts an integral iron core injection molding process. The core workstations include key processes such as robot handling, insertion of magnetic steel into iron cores, injection molding, rotor into shaft, press-fitting, magnetization, oil spraying, dynamic balance, and detection. The whole line is highly automated to ensure the assembly accuracy and consistency and meet the high-performance requirements of electric motors for new energy vehicles, providing an efficient and reliable production solution
Core Station Composition
Robot handling, insertion of magnetic steel into iron cores, injection molding of iron cores, stacking of iron cores, rotor into shaft, press-fitting of rings, press-fitting of bearings, spraying of rotor with oil, magnetization of rotor, detection of surface magnetic field, height detection, dynamic balance detection, laser marking
Technical Highlights
The assembly process is mainly automatic, and the production line automation rate is 85%. Two products can be switched for production
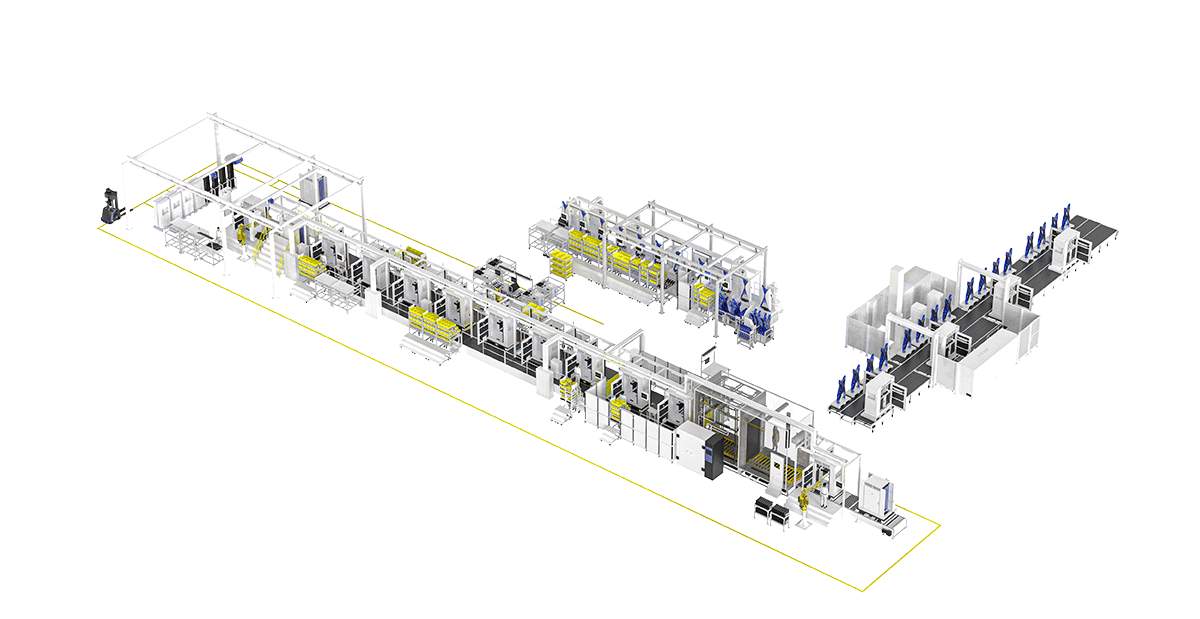
Charging Pile Assembly / Test Line
The assembly and test line for new energy vehicle charging piles consists of a host assembly test line, a terminal assembly test line, and a whole machine test line. The whole line uses customized chain plates for the transmission of charging pile products, and materials are supplied automatically by AGV to ensure an efficient and automated production process. It is dedicated to manufacturing super DC charging piles to meet the high-power charging requirements in the field of new energy vehicles
Core Station Composition
Core workstations include host on-line, distribution module installation, electrical inspection, rain test, terminal on-line, safety regulation testing, airtightness testing, ATE (Automated Test Equipment) testing, aging testing, etc
Technical Highlights
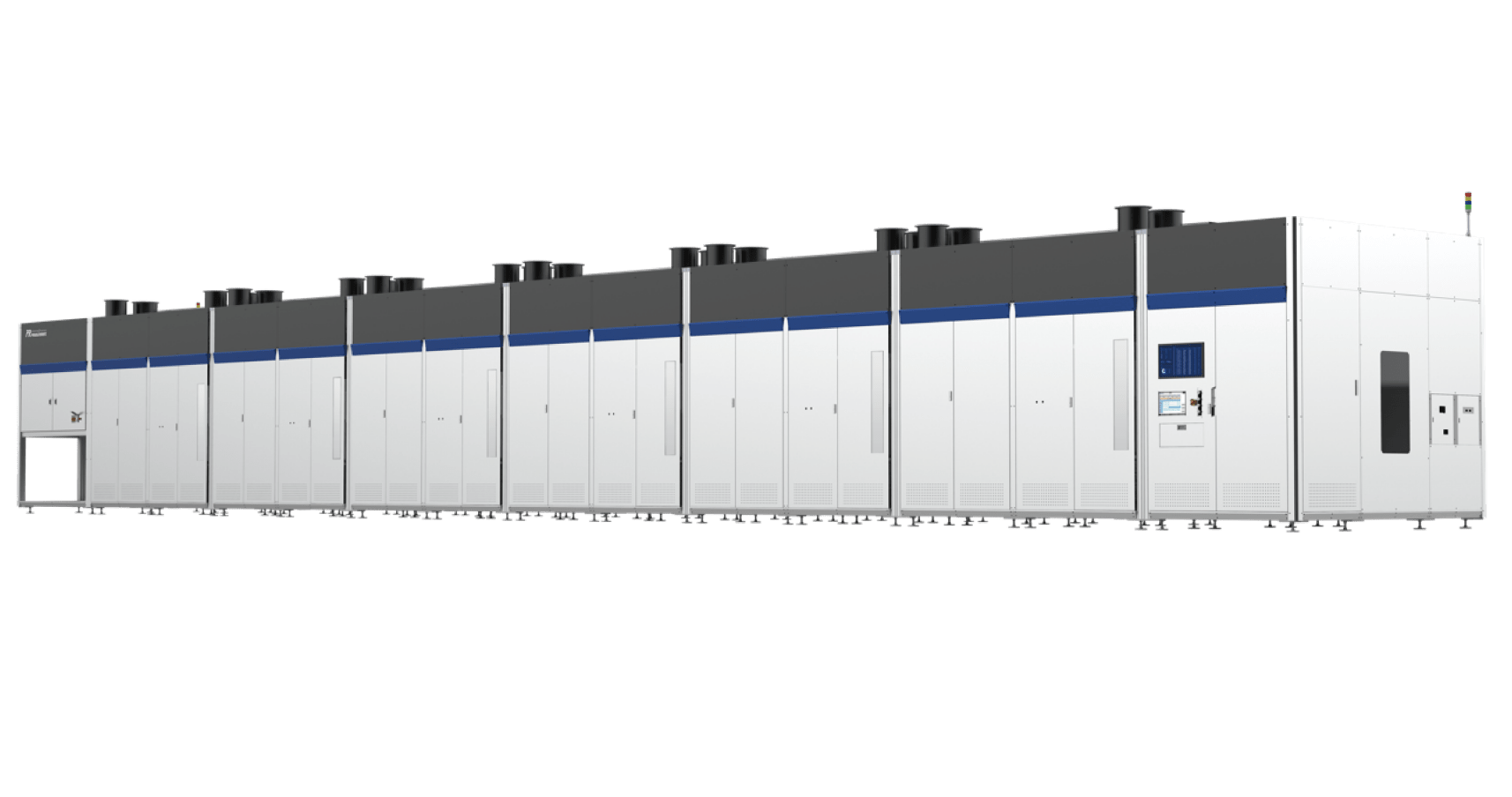
High-Temperature Fully Automated Burn-In Test Line
The?High-Temperature Fully Automated Burn-In Test Line?is specifically engineered for the electronic control systems of new energy vehicles (NEVs). Utilizing high power-density power supplies, RGVs (Rail Guided Vehicles), and automated curing ovens, the system enables high-temperature burn-in testing. This process accelerates product response mechanisms, effectively eliminates potential defects, and significantly enhances product quality and reliability

Electromechanical Brake (EMB) Assembly / Test Line
The EMB assembly and test line is composed of the EMB housing assembly line and the EMB bracket and assembly test line. It is dedicated to producing high-performance electromechanical and software-integrated braking products. The whole line integrates automated assembly and testing technologies to ensure accurate assembly, performance reliability, and quality consistency of products, meeting the high-standard production requirements of braking systems for new energy vehicles
Core Station Composition
Screw assembly, MGU installation, assembly airtightness testing, sliding force testing, drag torque testing, profile detection, assembly EOL testing, etc
Technical Highlights
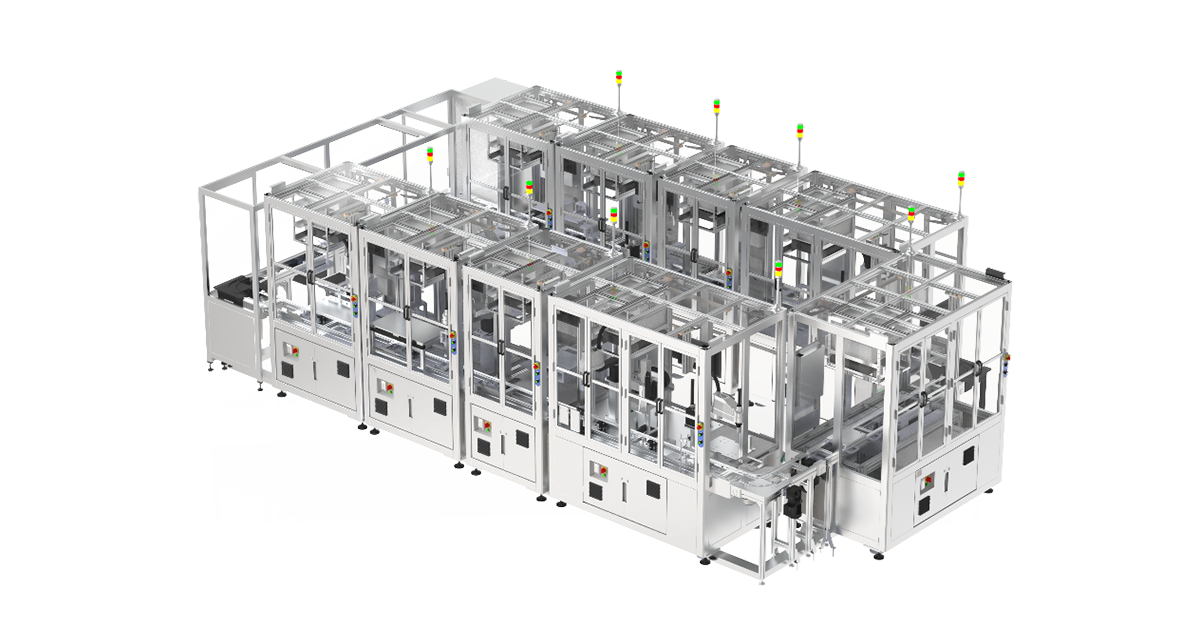
EPB MGU Assembly / Test Line
The EPB MGU assembly and test line adopts a circular double-speed chain design and is dedicated to producing high-performance EPB MGU products. The whole line integrates advanced automated assembly and testing technologies to ensure strict requirements in terms of product performance, quality, and consistency, improve production efficiency and precision, and provide a high-standard braking system solution for new energy vehicles
Core Station Composition
Motor gear press-fitting, motor end cover welding, resistance welding, laser welding, performance testing, noise testing, etc
Technical Highlights
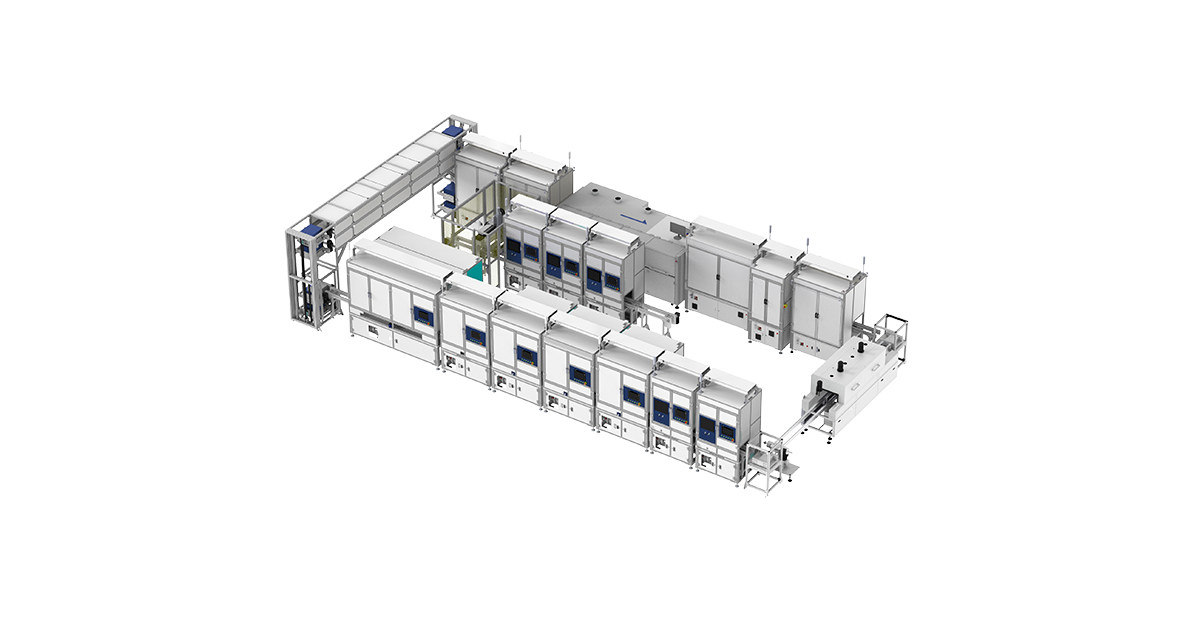
ECU Assembly / Test Line
The ECU assembly and test line is composed of the PCBA test sub-line and the ECU main line. It is dedicated to producing the core component ECU of the automotive Onebox brake-by-wire system. The whole line integrates automated testing and assembly technologies to ensure high precision and reliability of products, meeting the strict performance requirements of the automotive braking system for core components and facilitating efficient production and quality control
Core Station Composition
Program burning, FCT testing, ultrasonic welding of breathable film, selective wave soldering, dispensing and pressing of case cover, etc
Technical Highlights
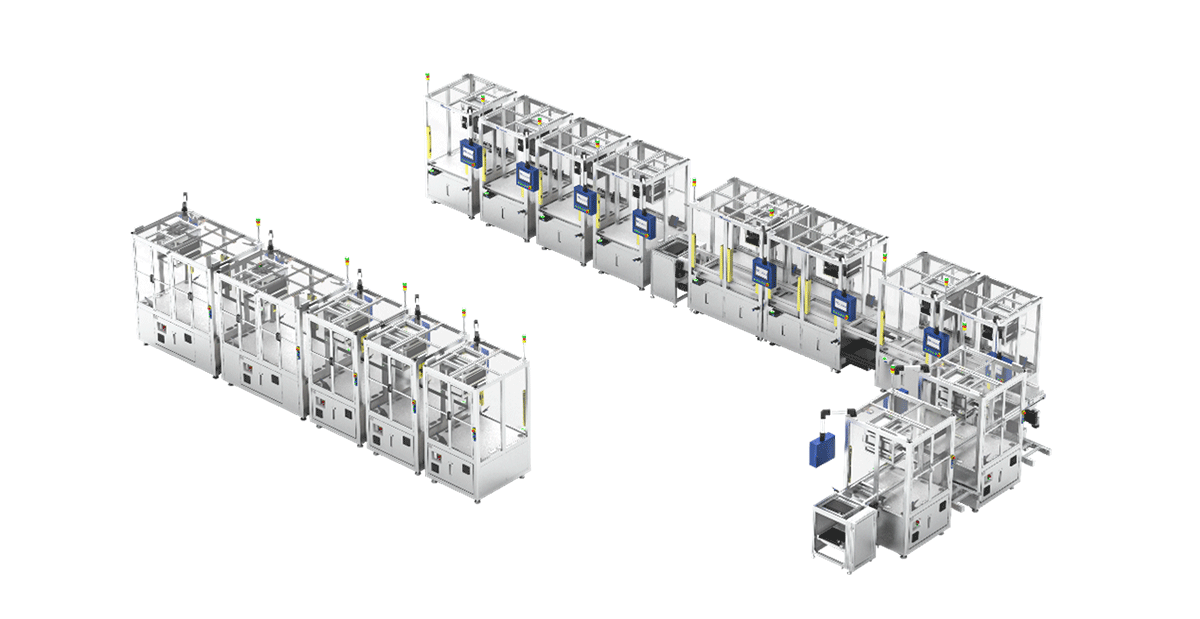
SBW Assembly / Test Line
The SBW-HWA assembly and test line is composed of an off-line controller line, an off-line upper and lower HWA semi-finished product line, and a main line assembly and test line. It is dedicated to producing the core component of the automotive steer-by-wire system – the haptic simulator. The whole line integrates advanced assembly and testing technologies to ensure high precision and consistency of products, meet the strict performance requirements of the automotive steer-by-wire system for key components, and support efficient production and quality control
Core Station Composition
Motor installation, angle sensor installation, tension testing, stroke component installation, angle component installation, EOL & NVH testing, etc
Technical Highlights

EMB/EPB Performance Test Bench
The?EMB/EPB Performance Test Bench?is designed to perform functional testing of EMB/EPB assemblies, providing an initial assessment of compliance with vehicle braking safety requirements. The system features a modular design and consists of a control cabinet, rigid displacement test bench,sliding resistance test bench , drag torque test bench, sub-assembly efficiency test bench, high-low temperature chamber, and hydraulic pump station. It also supports traditional brake caliper testing functions
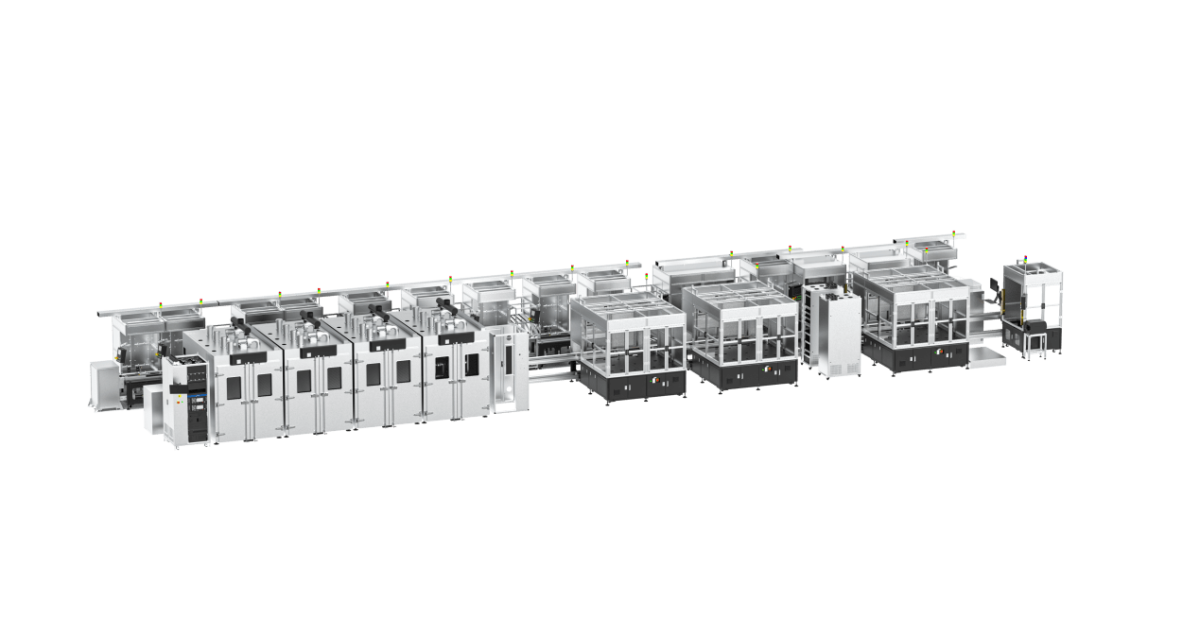
Cockpit Domain Controller Assembly / Test Line
It is an automated production line designed for efficient and precise assembly of intelligent cockpit controllers. It integrates advanced automation technology, sophisticated mechanical structures, intelligent control systems and stringent quality management systems to improve productivity, reduce labor costs and ensure product quality stability and consistency. Key features include high automation, high flexibility, high reliability, and good scalability for different assembly models
Core Station Composition
Laser marking, automatic feeding, tightening, dispensing, airtightness detection, abnormal noise testing
Technical Highlights
Strong compatibility, high flexibility, high reliability, and scalability
Cockpit Domain
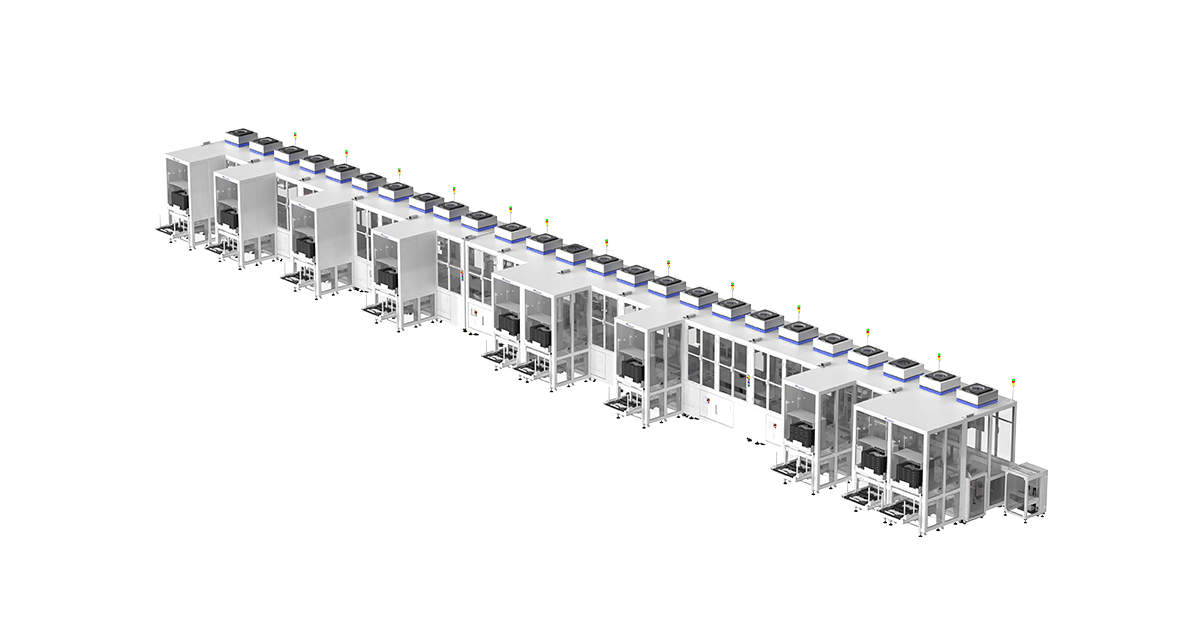
Radar Assembly / Test Line
The lidar assembly line has excellent product compatibility. It adopts a tray feeding system to ensure efficient and stable material supply. The core processes of the whole line are 100% automated to ensure high quality and high efficiency of on-board lidars. Advanced automation technology improves production efficiency, meets strict quality standards, and flexibly adapts to assembly needs of different models, enhancing production flexibility and scalability
Core Station Composition
Automatic dispensing, automatic solder paste dispensing, solder joint detection, motor assembly, and tightening of the rotating mirror semi-finished product assembly
Technical Highlights
ADCU Assembly and Test Line
The?ADCU (Autonomous Driving Domain Control Unit) Assembly and Test Line?consists of automated workstations for material loading, screw fastening, dispensing, functional testing, IMU (Inertial Measurement Unit) calibration, GPS navigation testing, coolant channel air-tightness testing, end-of-line (EOL) testing, and application programming/burn-in testing. The line is purpose-built for efficient and high-precision production of autonomous driving domain controllers
Intelligent Driving
Electronic Control / Inverter Brick Assembly / Test Line
Electronic Control / Inverter Brick Assembly / Test Line
The assembly and test line for electronic control/inverter bricks of new energy vehicles realizes fully automated and flexible production, integrating processes such as loading and unloading, assembling, dispensing, potting, curing, testing, and aging. The whole line adopts a visual production kanban system to monitor the process in real time and record data throughout the process to ensure traceability. The flexible and quick-change design supports rapid adjustment to meet the efficient production needs of different products
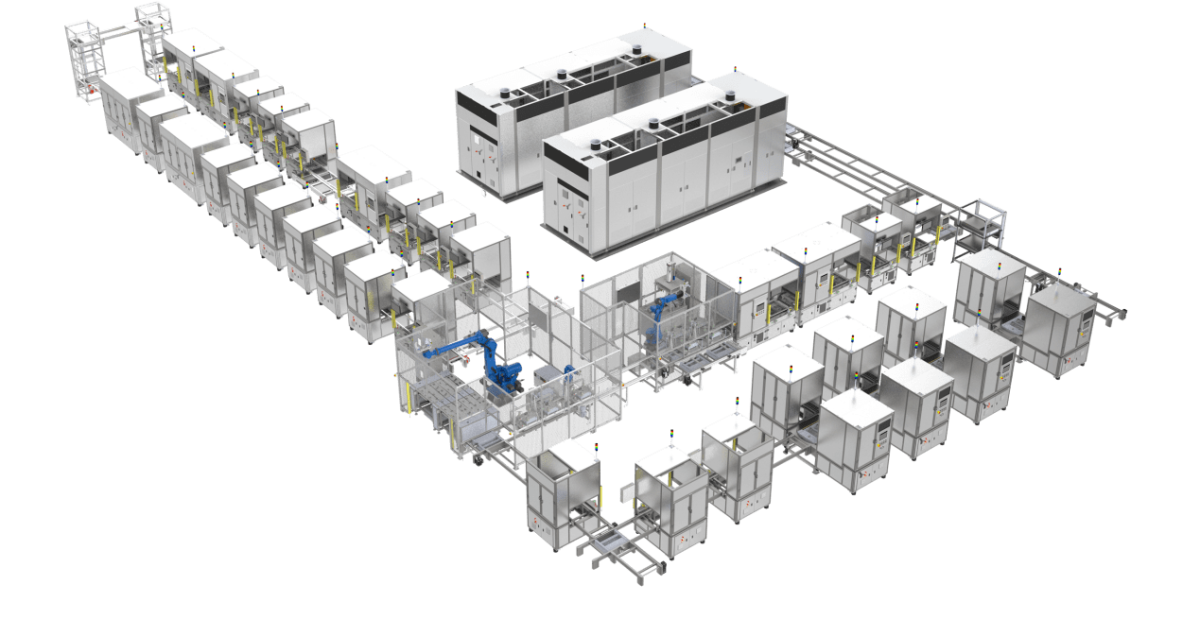
Core Station Composition
Tightening, dispensing, curing, wave soldering, AOI (Automated Optical Inspection), airtightness testing, aging testing, safety regulation testing, EOL testing
Technical Highlights
Modular and flexible design, visualization, automatic screening of OK and NG products, and traceability of the source of defects
OBC DCDC Assembly / Test Line
The assembly and test line for new energy vehicle OBC/DCDC integrates mechanical, electrical and control technologies to realize the automatic transportation, assembly and detection of electronic control components. Through advanced equipment and strict testing, the product performance is comprehensively evaluated, such as data processing, power consumption, stability and reliability. The intelligent control system monitors and adjusts production parameters in real time to ensure that each product is assembled and tested under the best conditions, providing efficient guarantee for the production of new energy vehicles
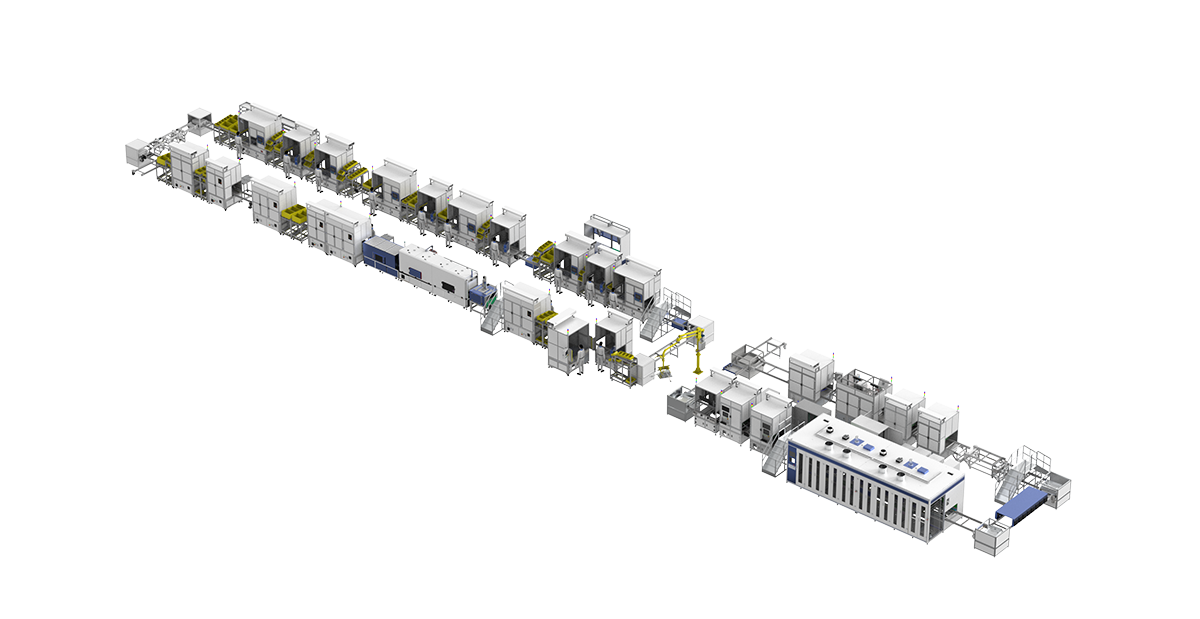
Core Station Composition
Selective soldering, tightening, dispensing, curing, AOI (Automated Optical Inspection), three-proof coating, abnormal sound testing, safety regulation testing, calibration testing
Technical highlights
High-precision assembly, highly efficient automated production, flexible and customizable, intelligent management
Electric Drive Assembly / Test Line
The electric drive assembly and test line for new energy vehicles integrates advanced automated assembly and detection technologies, covering processes such as assembly, press-fitting, tightening, oil injection, electrical performance detection, and EOL testing. Through a highly automated and flexible design, the whole line ensures efficient production and precise quality control. The intelligent production management system can monitor the production status in real time and dynamically adjust process parameters to ensure the assembly accuracy and reliability of products, providing a stable technical guarantee for the electric drive system of new energy vehicles
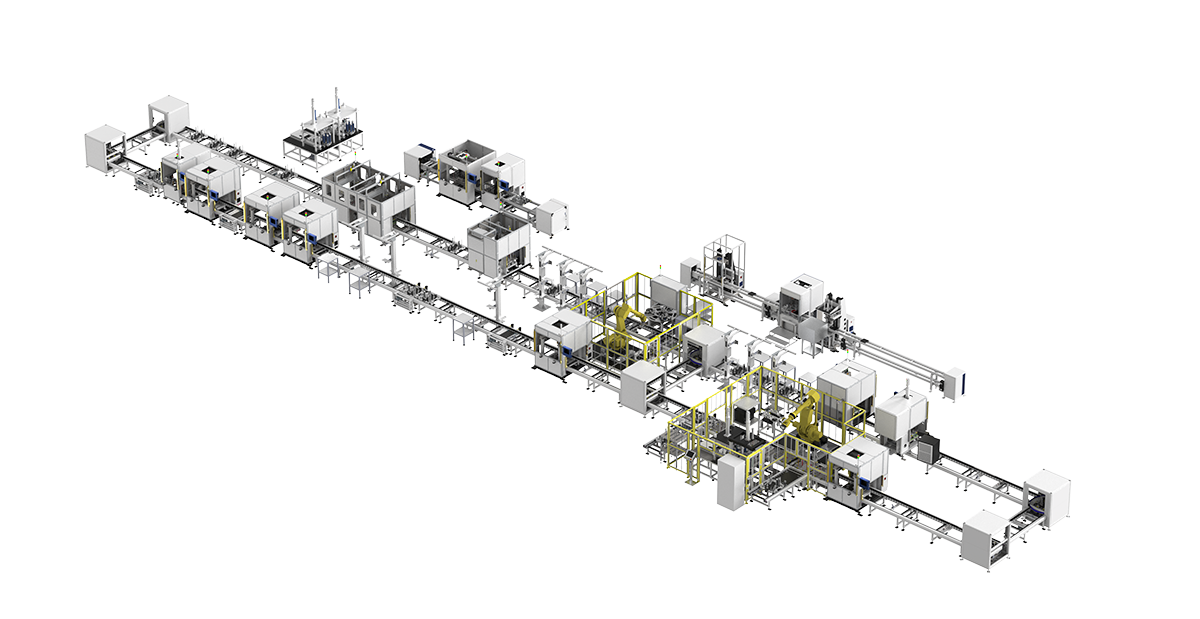
Core Station Composition
Starting resistance torque test, automatic press-fitting of elastic pins, heating equipment for driven gears, tightening of differential bolts, press-fitting of inner rings of differential bearings, differential, press-fitting of outer rings of secondary shafts, measurement and selection of shims, assembly of shaft systems into boxes, tightening of hydraulic modules, tightening of box bolts, oil injection and extraction and weighing, electrical performance testing, EOL testing
Technical Highlights
The assembly process is mainly automatic, and the automation rate of the production line is 80%. Two products can be switched for production
Electric Motor Assembly/Test Line
The electric motor assembly and test line for new energy vehicles has an annual production capacity of 150,000 flat wire motors. It adopts a modular and lightweight design and supports multi-linear production and rapid model change. The whole line integrates advanced automated technologies to ensure the accuracy and consistency of assembly and flexibly respond to different product requirements, improving production efficiency. It provides an efficient and reliable production solution for the power system of new energy vehicles
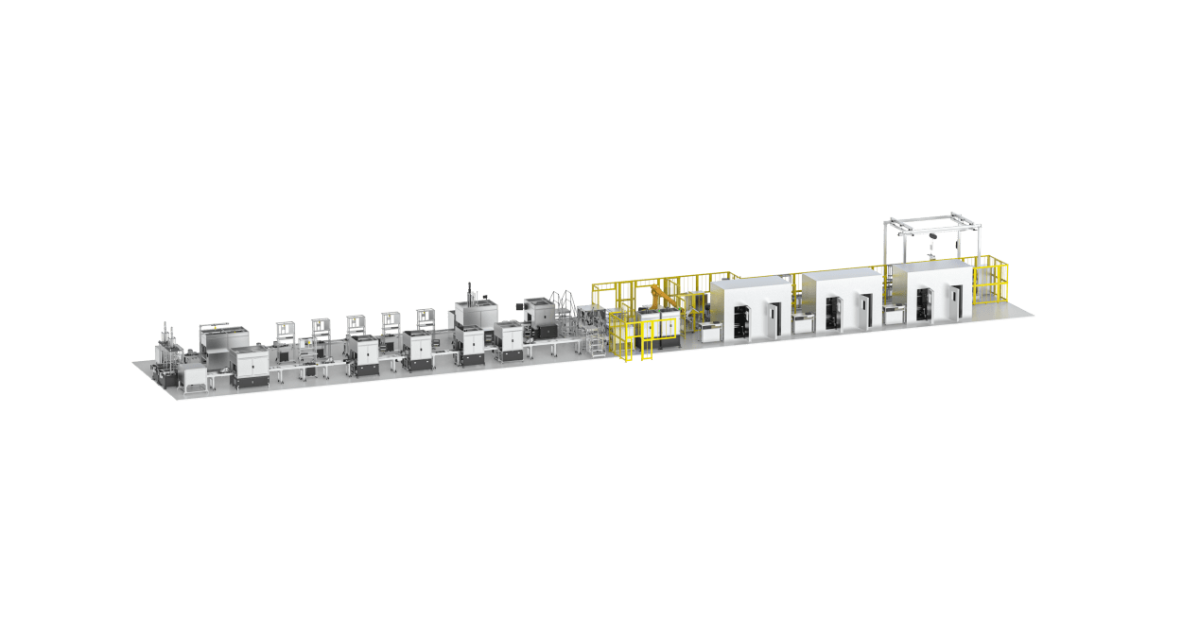
Core Station Composition
Riveting/pressing/dispensing of iron cores, stacking into shafts, dynamic balance testing, rotor into end cap, whole machine assembly, dispensing on housing, tightening of screws for assembly, dispensing on small end cap surface, heat shrinking stator, comprehensive testing, airtightness testing, no-load testing in a silent room
Technical Highlights
The assembly process is mainly automatic, and the automation rate of the production line is 85%. Three products can be switched for production
Rotor Assembly / Test Line
The rotor assembly and test line for new energy vehicles adopts an integral iron core injection molding process. The core workstations include key processes such as robot handling, insertion of magnetic steel into iron cores, injection molding, rotor into shaft, press-fitting, magnetization, oil spraying, dynamic balance, and detection. The whole line is highly automated to ensure the assembly accuracy and consistency and meet the high-performance requirements of electric motors for new energy vehicles, providing an efficient and reliable production solution
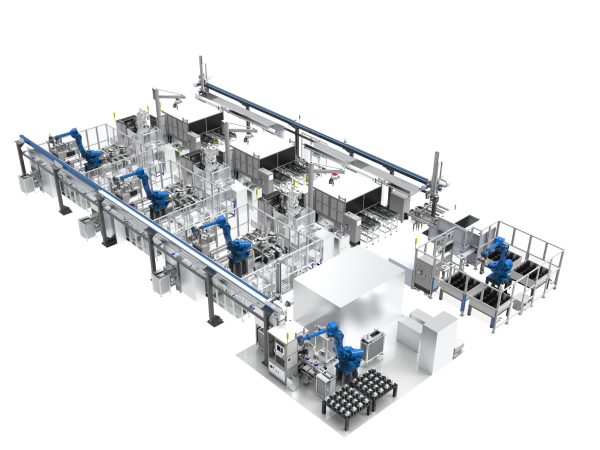
Core Station Composition
Robot handling, insertion of magnetic steel into iron cores, injection molding of iron cores, stacking of iron cores, rotor into shaft, press-fitting of rings, press-fitting of bearings, spraying of rotor with oil, magnetization of rotor, detection of surface magnetic field, height detection, dynamic balance detection, laser marking
Technical Highlights
The assembly process is mainly automatic, and the production line automation rate is 85%. Two products can be switched for production
Charging Pile Assembly / Test Line
The assembly and test line for new energy vehicle charging piles consists of a host assembly test line, a terminal assembly test line, and a whole machine test line. The whole line uses customized chain plates for the transmission of charging pile products, and materials are supplied automatically by AGV to ensure an efficient and automated production process. It is dedicated to manufacturing super DC charging piles to meet the high-power charging requirements in the field of new energy vehicles
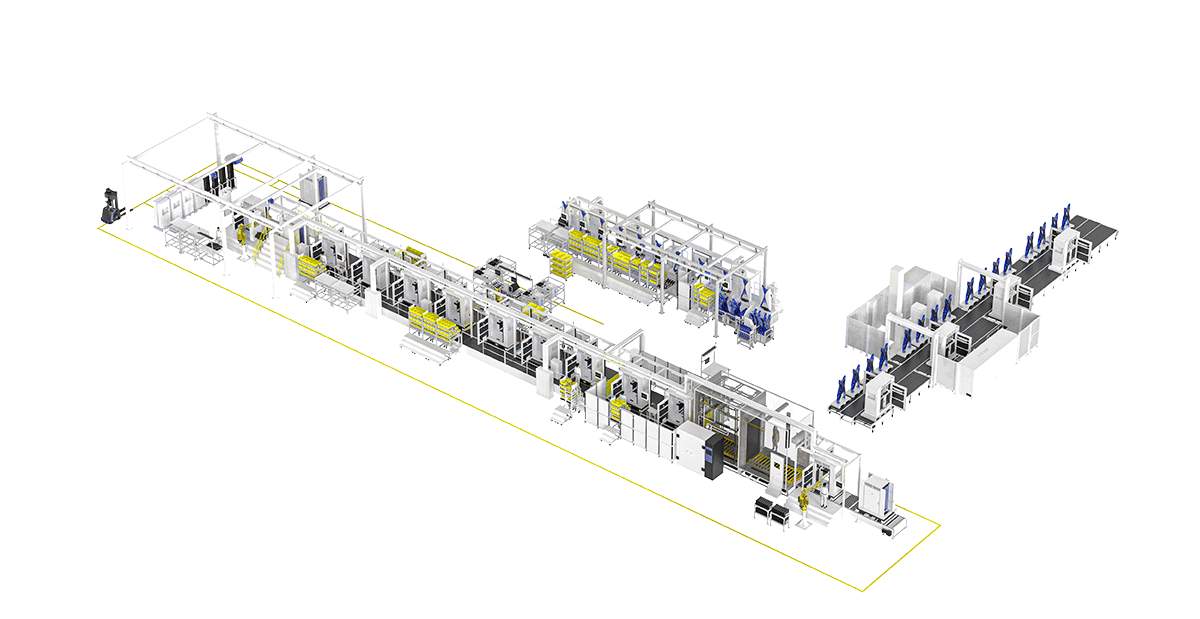
Core Station Composition
Core workstations include host on-line, distribution module installation, electrical inspection, rain test, terminal on-line, safety regulation testing, airtightness testing, ATE (Automated Test Equipment) testing, aging testing, etc
Technical Highlights
High-Temperature Fully Automated Burn-In Test Line
The?High-Temperature Fully Automated Burn-In Test Line?is specifically engineered for the electronic control systems of new energy vehicles (NEVs). Utilizing high power-density power supplies, RGVs (Rail Guided Vehicles), and automated curing ovens, the system enables high-temperature burn-in testing. This process accelerates product response mechanisms, effectively eliminates potential defects, and significantly enhances product quality and reliability
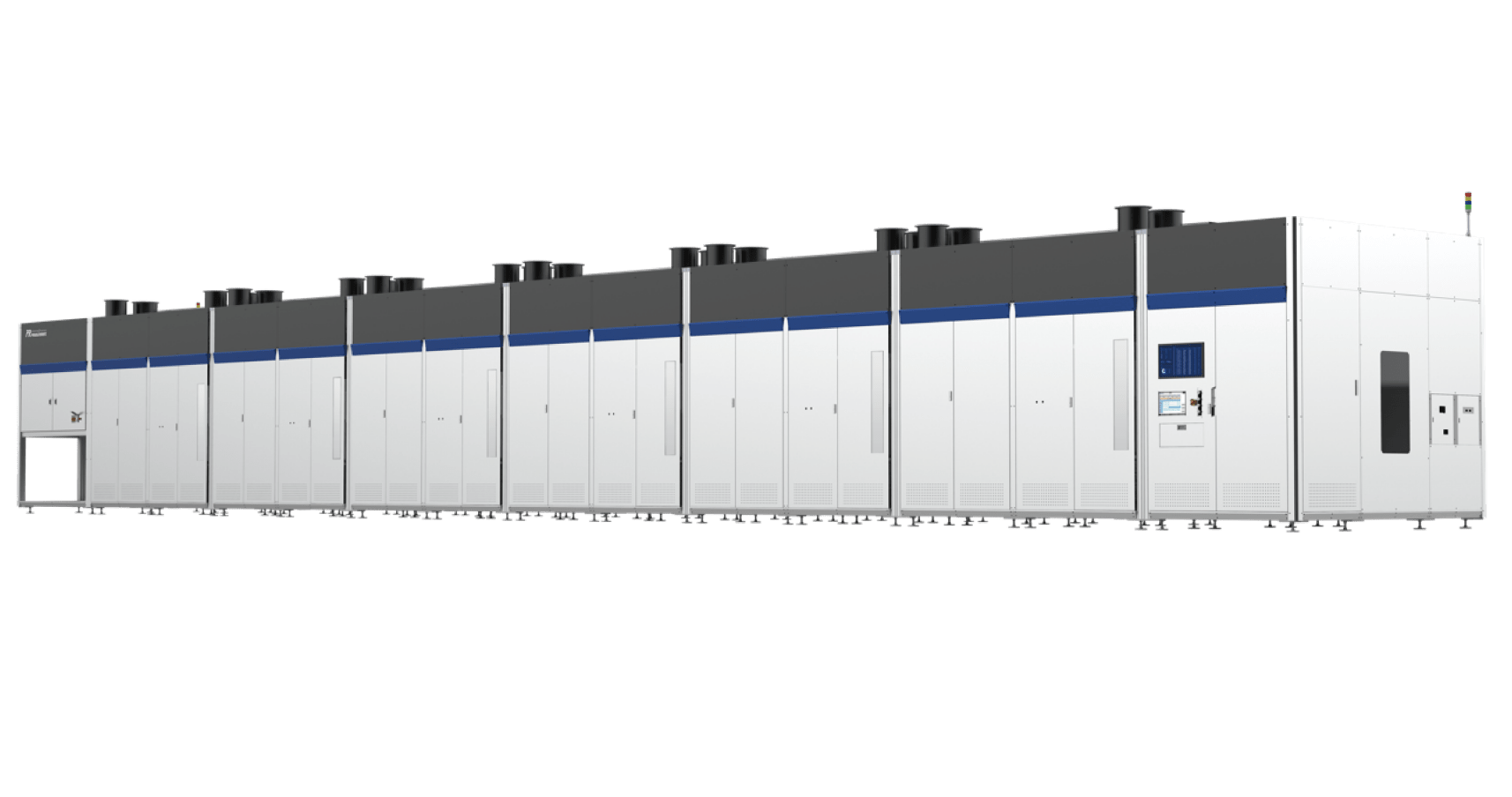
Electromechanical Brake (EMB) Assembly / Test Line
Electromechanical Brake (EMB) Assembly / Test Line
The EMB assembly and test line is composed of the EMB housing assembly line and the EMB bracket and assembly test line. It is dedicated to producing high-performance electromechanical and software-integrated braking products. The whole line integrates automated assembly and testing technologies to ensure accurate assembly, performance reliability, and quality consistency of products, meeting the high-standard production requirements of braking systems for new energy vehicles

Core Station Composition
Screw assembly, MGU installation, assembly airtightness testing, sliding force testing, drag torque testing, profile detection, assembly EOL testing, etc
Technical Highlights
EPB MGU Assembly / Test Line
The EPB MGU assembly and test line adopts a circular double-speed chain design and is dedicated to producing high-performance EPB MGU products. The whole line integrates advanced automated assembly and testing technologies to ensure strict requirements in terms of product performance, quality, and consistency, improve production efficiency and precision, and provide a high-standard braking system solution for new energy vehicles
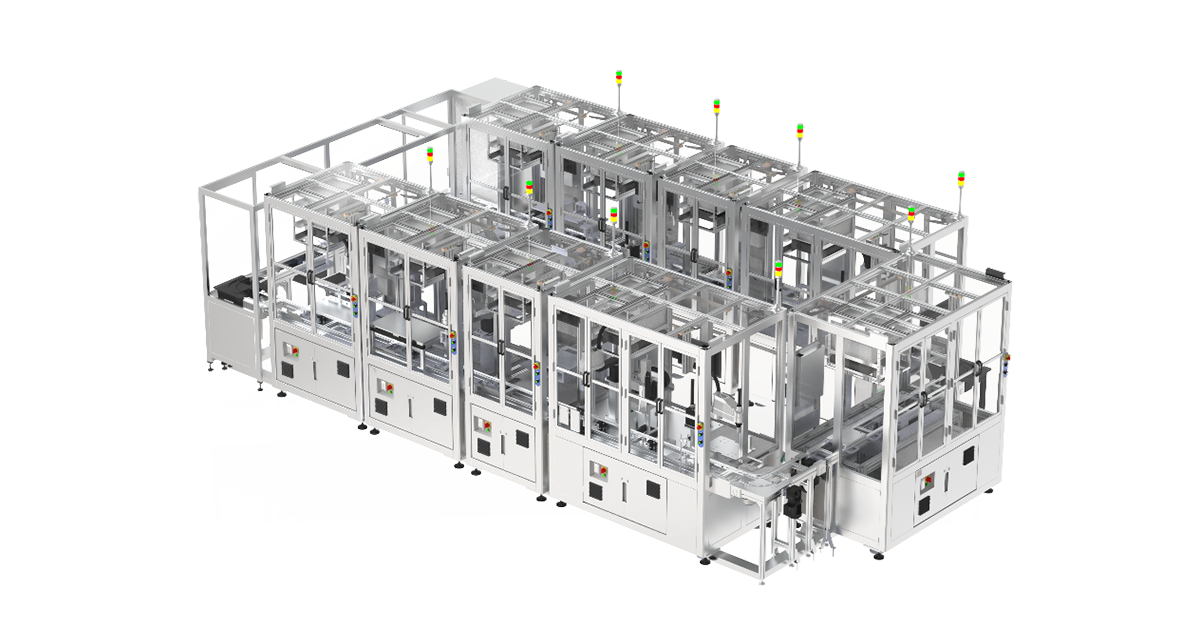
Core Station Composition
Motor gear press-fitting, motor end cover welding, resistance welding, laser welding, performance testing, noise testing, etc
Technical Highlights
ECU Assembly / Test Line
The ECU assembly and test line is composed of the PCBA test sub-line and the ECU main line. It is dedicated to producing the core component ECU of the automotive Onebox brake-by-wire system. The whole line integrates automated testing and assembly technologies to ensure high precision and reliability of products, meeting the strict performance requirements of the automotive braking system for core components and facilitating efficient production and quality control
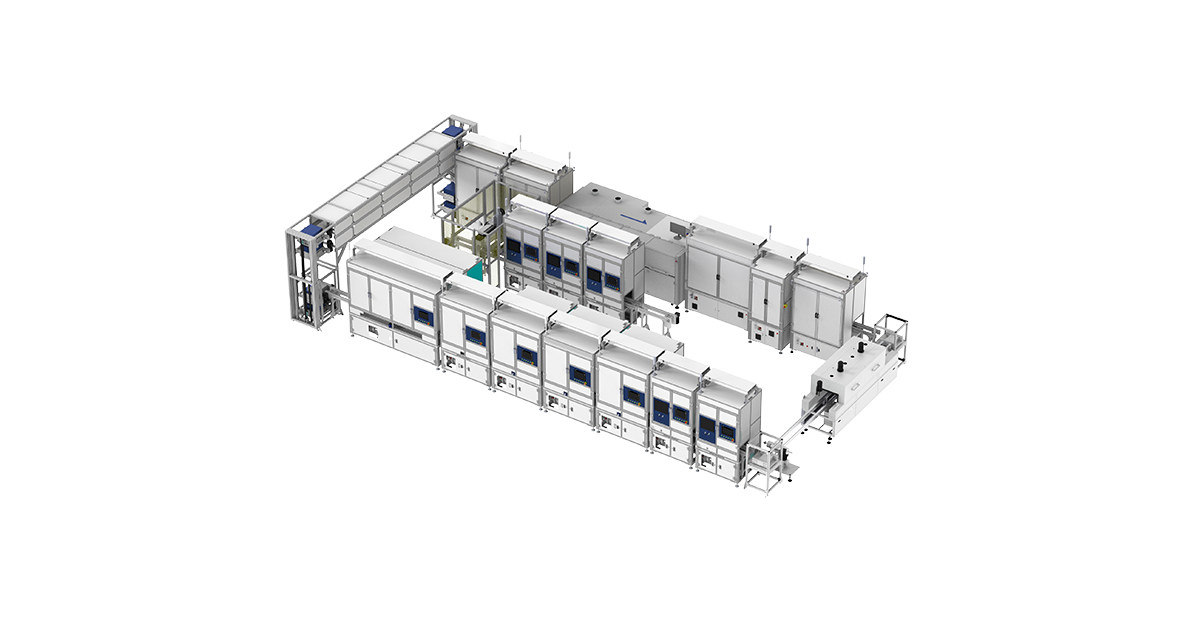
Core Station Composition
Program burning, FCT testing, ultrasonic welding of breathable film, selective wave soldering, dispensing and pressing of case cover, etc
Technical Highlights
SBW Assembly / Test Line
The SBW-HWA assembly and test line is composed of an off-line controller line, an off-line upper and lower HWA semi-finished product line, and a main line assembly and test line. It is dedicated to producing the core component of the automotive steer-by-wire system – the haptic simulator. The whole line integrates advanced assembly and testing technologies to ensure high precision and consistency of products, meet the strict performance requirements of the automotive steer-by-wire system for key components, and support efficient production and quality control
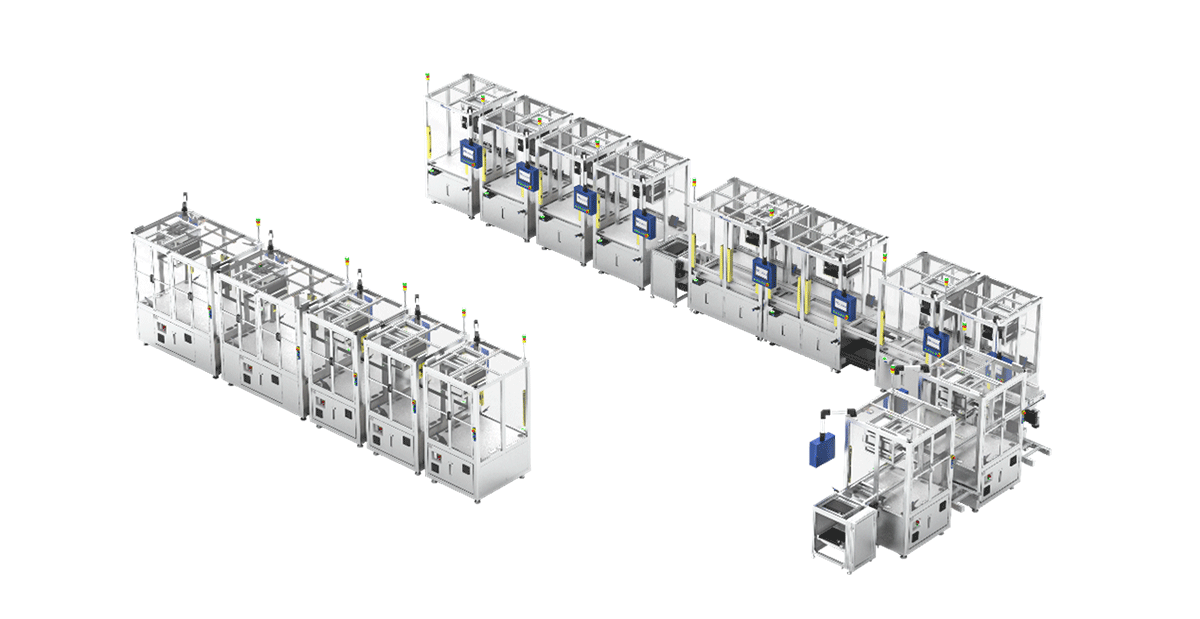
Core Station Composition
Motor installation, angle sensor installation, tension testing, stroke component installation, angle component installation, EOL & NVH testing, etc
Technical Highlights
EMB/EPB Performance Test Bench
The?EMB/EPB Performance Test Bench?is designed to perform functional testing of EMB/EPB assemblies, providing an initial assessment of compliance with vehicle braking safety requirements. The system features a modular design and consists of a control cabinet, rigid displacement test bench,sliding resistance test bench , drag torque test bench, sub-assembly efficiency test bench, high-low temperature chamber, and hydraulic pump station. It also supports traditional brake caliper testing functions

Cockpit Domain Controller Assembly / Test Line
Cockpit Domain
Cockpit Domain Controller Assembly / Test Line
It is an automated production line designed for efficient and precise assembly of intelligent cockpit controllers. It integrates advanced automation technology, sophisticated mechanical structures, intelligent control systems and stringent quality management systems to improve productivity, reduce labor costs and ensure product quality stability and consistency. Key features include high automation, high flexibility, high reliability, and good scalability for different assembly models
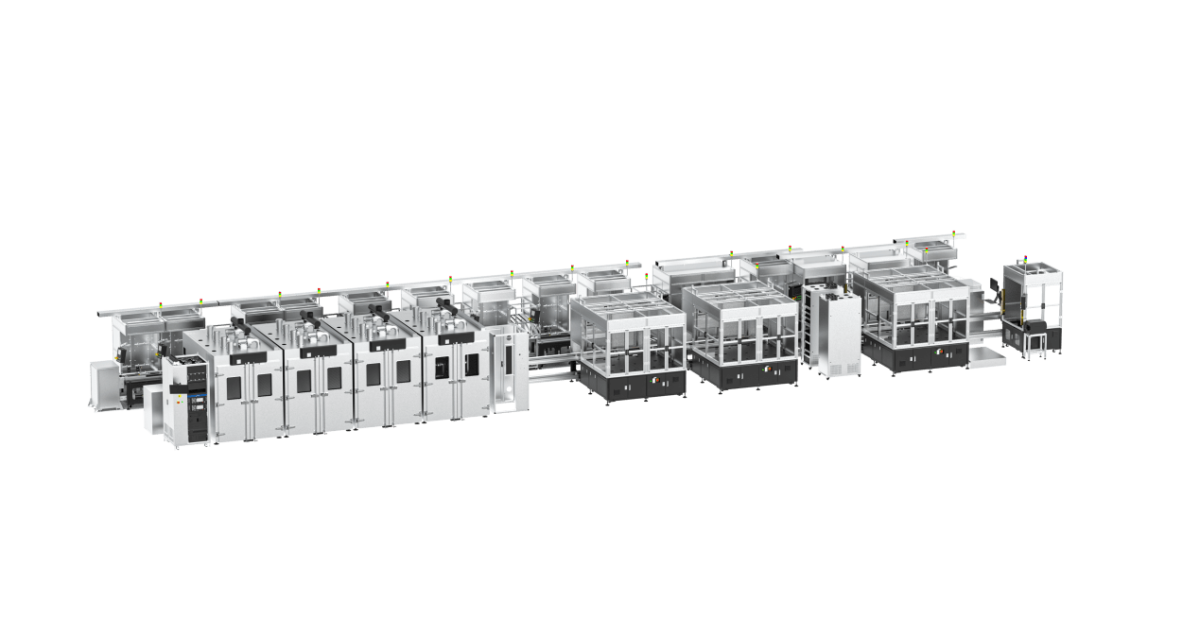
Core Station Composition
Laser marking, automatic feeding, tightening, dispensing, airtightness detection, abnormal noise testing
Technical Highlights
Strong compatibility, high flexibility, high reliability, and scalability
Radar Assembly / Test Line
Intelligent Driving
Radar Assembly / Test Line
The lidar assembly line has excellent product compatibility. It adopts a tray feeding system to ensure efficient and stable material supply. The core processes of the whole line are 100% automated to ensure high quality and high efficiency of on-board lidars. Advanced automation technology improves production efficiency, meets strict quality standards, and flexibly adapts to assembly needs of different models, enhancing production flexibility and scalability
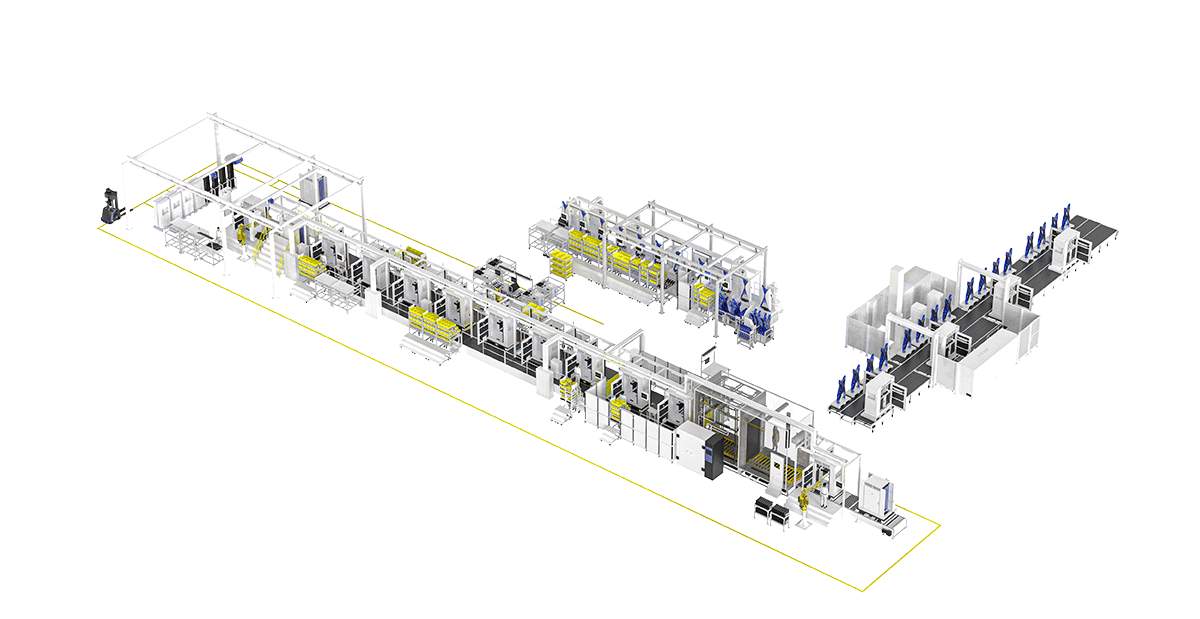
Core Station Composition
Automatic dispensing, automatic solder paste dispensing, solder joint detection, motor assembly, and tightening of the rotating mirror semi-finished product assembly
Technical Highlights
ADCU Assembly and Test Line
The?ADCU (Autonomous Driving Domain Control Unit) Assembly and Test Line?consists of automated workstations for material loading, screw fastening, dispensing, functional testing, IMU (Inertial Measurement Unit) calibration, GPS navigation testing, coolant channel air-tightness testing, end-of-line (EOL) testing, and application programming/burn-in testing. The line is purpose-built for efficient and high-precision production of autonomous driving domain controllers